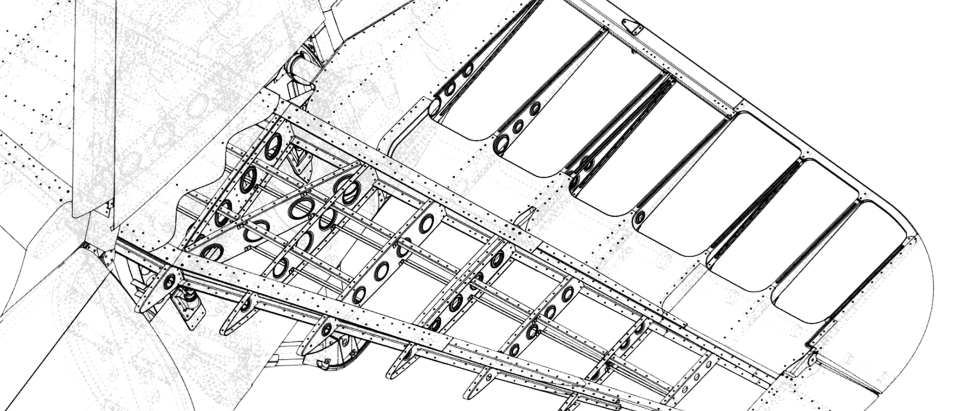
’80-urile au fost dezmembrate fără milă, fabrica a dispărut, documentaţia s-a risipit şi oamenii care le-au construit sau zburat, ne-au părăsit treptat. Au ramas amintiri şi legende, fotografii cu patina vremii, filmuleţe cu iz de război, un mare gol şi un mare regret. Dar ’80-ul nu a încetat să existe în sufletele românilor. De-a lungul timpului nu a existat generație care să nu fi visat la posibilitatea construirii din nou a unui IAR 80.
Realizarea unei replici scara 1:1 a avionului IAR 80 în condiții de zbor, este posibilă numai printr-un efort susținut al unei echipe de specialiști entuziaști, cu bune cunoștințe în proiectare, fabricație, testare, întreținere și zbor. Întregul proiect este conceput pe bază de voluntariat dar, pentru realizarea avionului este necesar sprijinul unor sponsori care să contribuie la finanțarea cumpărării materialelor și a cheltuielilor de proiectare, testare și funcționare.
1. Obiectivele proiectului :
-
Construcția unui avion care să zboare în condiții de maximă siguranță și care îndeplinește condițiile de certificare la clasa avioane istorice;
-
Să respecte cât mai mult planurile originale;
-
Să fie sustenabil din punct de vedere al mentenanței.
2. Proiectare:
Activitatea de documentare desfășurată pe parcursul a 3 ani a dus la identificarea a aproape 200 de desene de ansamblu originale, majoritatea de structură, a manualului de întreținere, a manualului de zbor, a catalogului ilustrat cu piese de schimb, etc. O parte din ele sunt disponibile in rubrica „Documentație” de pe site. Pentru studiu și documentare mai există câteva piese originale: un ampenaj orizontal, fragmente de lonjeroane, tren, etc;
În mod natural pasul următor a fost „învățarea avionului” și definirea unei configurații posibile prin selectarea unor echipamente disponibile pe piață: motor, elice, tren de aterizare, instalații. Elaborarea caietului de sarcini pentru IAR 80 R, s-a făcut pe următoarele principii :
-
Se va realiza o structură cât mai apropiată de structura originală a avionului;
-
Varianta de motorizare este Pratt & Whitney R 1830 cu elice Hamilton (variante folosite pe DC 3, B 24), încă disponibil pe piață , certificat FAA după RK;
-
Se va adapta un tren de aterizare de la un avion T 28 Trojan , disponibil cu certificat FAA;
-
Se vor utiliza numai echipamente noi sau reparate cu certificare FAA pentru instalații, cât mai asemănătoare cu cele originale. Certificarea FAA este necesară pentru echipamentele importate din SUA, unde există cea mai mare ofertă pentru această categorie de piese.
După aceste studii preliminare, s-au întocmit un program al activităților și un buget estimativ. Calculele preliminare actuale, evidențiază că este nevoie de circa 22 000 ore proiectare CAD și 2 000 ore elaborare documentație pregătire de fabricație, manuale, fișe măsurători, nomenclatoare, instrucțiuni, etc. În total vor trebui realizate în jur de 3 000 desene.
3. Fabricație:
În mod normal costurile proiectării și a pregătirii de fabricație sunt distribuite pe un număr mare de exemplare produse. În cadrul acestui proiect s-a luat în calcul realizarea probabil a unui singur exemplar, motiv pentru care s-au căutat soluții constructive necostisitoare.
Principalele activități ale etapei de fabricație sunt:
-
Execuția SDV pentru fabricarea pieselor primare, în principal calapoade executate pe CNC;
-
Execuția pieselor primare din table pentru structură, majoritatea fiind realizate prin debitare, formare pe calapoade, stretching, abkant. Necesită tratamente termice, acoperiri de suprafață, în general echipamente specializate și scumpe, aflate doar în dotarea firmelor ce produc elemente de structuri de aviație;
-
Fabricarea pieselor frezate pe CNC;
-
Execuția SDV necesare asamblării structurii – gabarite;
-
Asamblarea în gabarite a principalelor elemente de structură;
-
Montajul echipamentelor și a componentelor pentru instalații;
-
Verificări, probe și teste la sol.
Abordarea propusă pentru minimizarea costurilor de fabricație:
-
Avionul va fi asamblat într-un atelier propriu (~350 m2), pentru a evita costurile indirecte mari specifice companiilor de mari dimensiuni;
-
Piesele care necesită procese specifice: frezare și debitare CNC, presare covor cauciuc, formare pe abkant, stretching, tratamente termice, NDT, acoperiri de suprafață, sudură, se vor executa prin colaborare cu firme de specialitate;
-
Pentru execuția calapoadelor pentru piese primare (aproximativ 600) , se va folosi MDF prelucrat CNC . Testele deja efectuate pentru presarea de nervuri din tabla pe presă cu covor cauciuc au demonstrat fezabilitatea pentru serii mici;
-
Gabaritele pentru asamblarea structurii vor fi fabricate în atelierul propriu;
-
Asamblarea principalelor elemente de structură, joncționarea, montajul general, testele și măsurătorile vor fi executate în atelierul propriu.
Bugetul estimativ pentru fabricație include un necesar de ~15000 ore manoperă directă pentru asamblarea structurii și instalații, plus, în principal orele de CNC. Restul de procese care necesită costuri mai mici vor fi determinate pe măsură ce sunt realizate desenele de execuție.
4. Fazele principale ale proiectului:
-
Realizarea întregii documentații în sistem CAD (vezi Planning);
-
Fabricarea unui ampenaj orizontal: calapoade, piese primare, gabarit, asamblare;
-
Elaborarea bugetului final pe baza costurilor înregistrate la producția ampenajului;
-
Obținerea sponsorizărilor necesare fabricației complete;
-
Fabricarea avionului complet;
-
Certificare, testare la sol și în zbor;
5. Concluzii:
-
Proiectul este fezabil. Avionul poate fi realizat pornind de la documentația originală existentă;
-
Este un proiect laborios, care necesită un volum mare de muncă de proiectare și fabricație:
-
24000 ore proiectare,
-
15000 ore manoperă directă,
-
un număr de ore mașină pentru operații specializate, ce va fi determinat pe măsura realizării proiectului.
-
-
Proiectul poate fi realizat prin angrenarea unui număr cât mai mare de specialiști cu experiență;