The IAR80R project aims to rebuild the Romanian IAR 80 aircraft, developed during the onset of World War II, being operational on the front between 1941-1945 and then as a training aircraft until 1952. After the war, the number of IAR80 aircraft decreased considerably, and there are currently no recovered, original copies. The main objective of the project is of historical restitution, offering to the general public in Romania, but also abroad, the opportunity to experience a historically accurate replica of the original IAR80 aircraft, in 3D virtual mock-up, in static and flight demonstrations. In this sense, important historical documents from the construction period of the aircraft (1939-1943) were recovered and these will largely constitute the foundation of the project.
The ‘Sky Legend’ Association updated the information and objectives within the IAR80R project, structured and planned from a budgetary and schedule point of view all the activities to be carried out in the project. Thus, a new Edition of the Statement of Work (SoW) was made and discussed within the Team.
The association, established in January 2019, initiated this project on a voluntary basis with history and technology enthusiasts, especially with the desire to recover the Romanian aviation technical history through specific activities, services or actions. The project was started from private initiatives and later integrated into the actions and purpose of the “SKY LEGEND” Association.
The evolution of the preliminary stages as well as the current situation of the project are illustrate din the following ‘Road map’:
- 2015 – The first private initiatives
- 2017 – The first technical measurements
- 2018 – The first Mock-up 1: 4 Solidworks scale
- 2018 – Creation of the SKY Legend Association
- 2019 – The first articles, interviews, production tests (technical activity, history, media)
- 2020 – Restructuring the Association and declaring the Purpose of the Project to the Romanian Aeronautical Authority
- 2020+ – Project Development (after the revised Specifications v 1.0 / 2020)
Roadmap IAR80R project
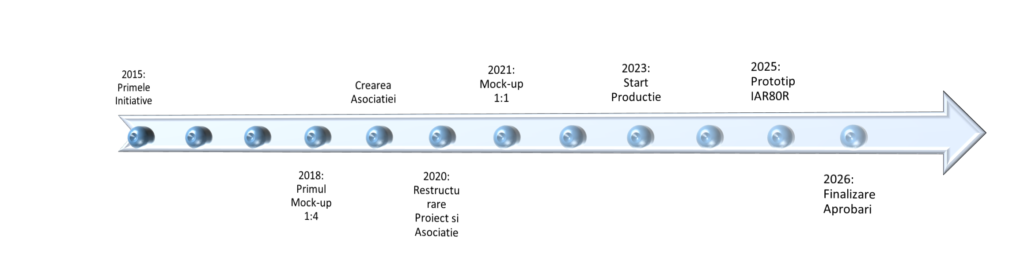
Scope and objectives of the project
According to the Statute, the ASSOCIATION aims to achieve the following objectives that fall within the scope of the IAR 80R aircraft project: retrieving the original information, creating a 3D model and creating a 1: 1 scale replica, functional, in airworthy condition.
Main purpose and objectives:
- Building up a documentation fund containing data and information related to the IAR 80 aircraft:
blueprints, manuals, books, drawings, photographs, films, etc. - Creating an accurate 3D Mock-up based on the original documentation
- Realization of the production documentation of the replica airplane and the associated manufacturing setup designed by the association members in collaboration with third parties
- Realization in collaboration with specialized companies of the IAR 80R aircraft
- Carrying out airworthiness ground and flight tests
- Aircraft registration, operation and participation in in-flight demonstrations
Project Structure
To allow for the diligent follow-up of such a unique, complex and long-lasting undertaking, the project has been broken down into several relevant work packages, with tasks that are easily identifiable, time bound and with well defined objectives. Alongside chapters such as Project Management and Communication and Media, which will take place throughout the project, the Technical chapter has been divided according to the specifics and complexity of the activities to be carried out.
The technical project will be structured in 3 main parts: ‘Design and Mock-up’, ‘Aircraft production’ and the continuous follow-up of ‘Quality and Safety’. Each of them contains an internal structure of specific work packages. With the exception of the recovery of the original technical documentation, the choice of the type variant for the 3D design and subsequent 1:1 prototype production, as well as the choice and acquisition of the engine and equipment, the activities associated with the 3 main technical will have a staggered start.
The project structure with its main chapters is presented graphically in the figure below:
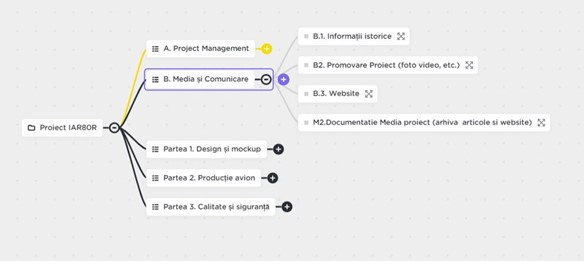
The Technical Project and the structuring of the objectives of each Technical Part were established taking into account their grouping as follows:
Part 1: ‘3D Design and Mock-up’ covers:
- Historical and technical documentation – Recovery of technical and historical documents, scanning, archiving, classifying, editing and transforming into usable format for 3D mpdelling
- 3D design – 3D models (made in Solidworks) according to the original and buildable variants
- CFD and FEM verification and validation calculations,
- Media and Communication – Historical articles, articles about the project activity and www presentation;
This part will cover mainly activities related to the design, 3D construction, analysis and verification as well as project technical documentation through voluntary participation of ‘Sky Legend’ members.
Part 2: ‘Production’ covers the preparation for production, the actual production and following maintenance steps:
- Pre-production information, production capacity and suppliers – Parts nomenclature, Supplier list
- Information and Engine acquisition – Engine acquisition (final phase)
- Design and preparation for procurement and production – 3D / 2D; production and procurement of parts, manufacturing & test tools and equipment
- Production – Delivery list, production
- Assembly and Installation – Logistics, components assembly and final aircraft delivery
- Design and purchase of equipment and machinery for maintenance and operation – Equipment, machinery for maintenance and operation
- Production and archiving documentation – Archive and project documents
- Media and Communication – Articles about the project manufacturing activities
Part 3: ‘Quality and safety’ covers quality and flight safety processes and their associated documentation as well as the mandatory airworthiness documentation. The maintenance phase, the technical project documentation (manuals) and the first airborne demonstrations at aviation events will be covered by this chapter.
- Quality documentation – Quality standards, Change Design list, Repairs and concessions
- Checks and measurements of quality and conformity – Verification documentation
- Technical documentation and manuals – Technical documentation (original ‘technical note’), Flight Manual
- Transport and maintenance – Transport and maintenance rules; Maintenance manual
- Airworthiness documentation – Ground and Flight Tests, Applications and Official Flight Authorization Documentation (Flight Certificate)
- Participation and preparation for Exhibitions and Meetings – Flight logs, Procedures, Documentation
- Project documentation and archiving – Archive and Project Documents
- Media and Communication – Articles, posts and www presence;
Project planning
The time given to the development of the project is also related to a number of risk factors. Not only the technical difficulties such as finding a compatible engine, the similarity and adaptation of hydraulic and electrical systems and installations, the production of a functioning aircraft and the necessary airworthiness approvals, but also the social risks such as: public interest in particular during the Covid pandemic and the gradual loss of the generation of the ´40s that developed and have flown this aircraft.
Taking into account the novelty of the project and the difficulties that may arise in any stage and chapter of it, the IAR 80R Project is expected to run for a minimum of 5 years. A short ‘Roadmap’ presentation is illustrated in the following chart:
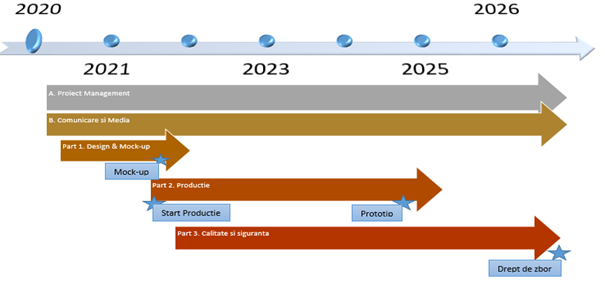
Project budget and costs
Regarding the Costs and Budget allocated to the project, for a first estimate we start from the following assumptions:
- Part P1. ‘Design and Mock-up’ and project organization will be sustained by the members of the Association in the form of active, voluntary involvement based on initiatives as well as experience, knowledge and skills.
- Part P2. Production and operation will be partially budgeted. It is considered that the acquisition of parts, their production, assembly as well as the maintenance and operation of the aircraft (product) will have to be financed. For this purpose, sponsorship contracts will be pursued, attracting investments to cover the necessary expenses. The aim is to involve partners in the project in the form of sponsorship or collaboration. Where appropriate, the level of involvement, interests or various other considerations will be concluded in collaboration agreements, partnerships or sponsorship agreements.
- Part P3. Quality and Safety will also be partially budgeted. The execution of ground and flight tests, as well as the expenses necessary for maintenance and operation but also the expenses with the necessary documentation for flight approvals and manuals will be included in the Project Costs. The aim is to obtain partnerships and sponsorships that can cover these expenses.
The estimated budget for the entire project includes the activity of Members and partners on a voluntary basis, which is estimated to no less than 14,000 hours. The costs of purchasing parts, installations, subassemblies or materials as well as the production and testing parts are initially estimated at a value of approx. 550,000 Euros. Collaborations, sponsorships and the active involvement of project partners are beneficial and encouraged in the project.
A novel historical finding, with the estimates of the project dating back to 1941, can be found in the IAR81 Spare Parts Catalogue (1941 edition):
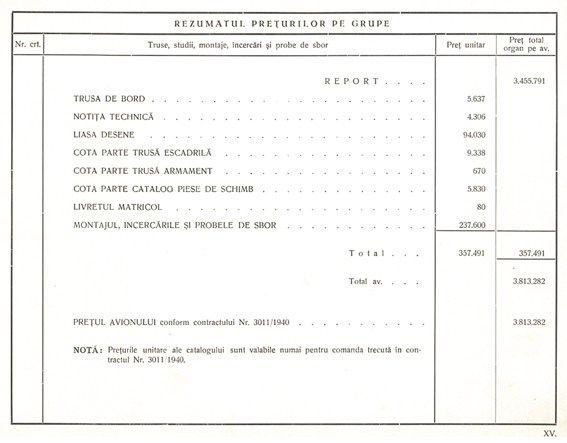
The Sky Legend Association, through the activity of the project, will make a major contribution to the recovery of the original documentation, its transformation into digital information, its preservation over generations and last but not least, making it available to the general public. Generations of aeronautical engineering students, but also the interested public will be able to experience a virtual 3D model of the plane that can be used for educational purposes and for the training of new engineers and aviation enthusiasts. The realization of a historically accurate 1:1 airworthy IAR 80/81 replica is the essence of the project contributing to the restitution of the historical heritage.
Our wish is for IAR 80R to become a proof of Romanian technical ingenuity and a source of inspiration for future generations of engineers, aviators and enthusiasts of technology and aviation in Romania and anywhere else in the world.
Author: MSc. Daniela Costăchescu